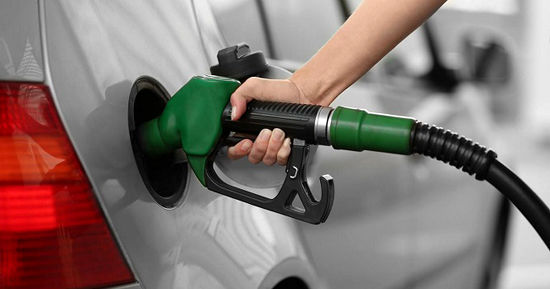
سامانه مانیتورینگ و ارسال دیتا به مرکز SCADA
برای کنترل سامانه های درایر- کمپرسور- دیسپتسر و تابلوهای F8G نیاز به یک سامانه HMI در اتاق کنترل هر جایگاه سوخت است. در صنعت اتوماسیون جایگاه های سوخت CNG از این سامانه به SMS یاد می شود. (Station Monitoring System)
پارامترهای کنترل در هر قسمت به صورت محلی در هر تابلو انتخاب می شود. ولی گزارش وضعیت سامانه از دیدگاه وضعیت پارامترهای کمپرسور- درایر- دیسپنسر و نشت گاز و شعله در یک نقطه به نام SMS انجام می شود. سامانه SMS قادر است علاوه بر جمع آوری اطلاعات کل سامانه با یک مودم؛ آن را در اختیار مرکز SCADA قرار دهد.
باید یک شبکه داخلی بین سامانه های کمپرسور- درایر- دیسپنسر و تابلوهای F8G برقرار باشد. بسته به نوع PLCها و شبکه های قابل پشتیبانی از طریق آنها می توان از شبکه Modbus. Ethernet و یا Profibus استفاده نمود. به دلیل قابلیت های فراوان در پروتکل Ethernet بهترین شبکه می تواند استفاده از این پروتکل باشد. سرعت بالا، پشتیبانی وسیع، امکانات وسیع، استفاده از این شبکه مزیت های نسبی این پروتکلند.
سامانه SMS باید قادر به ثبت وقایع و رویدادها و آلارم های سامانه باشد. هر رویداد با تاریخ و زمان و اتفاق آن باید ثبت گردد. منحنی دما و فشار کمپرسور نیز باید ترسیم گردد. سامانه SMS باید به UPS تجهیز شود تا در موقعی که برق در جایگاه قطع می شود قابلیت ادامه ارتباط با مرکز SCADA را داشته باشد.
پارامترهایی که از طریق SMS جمع آوری و در فواصل زمانی مشخص به مرکز SCADA ارسال می گردد در چهار قسمت قابل پی گیری است:
- مهمترین پارامترهای کمپرسور عبارتند از: میزان کارکرد کمپرسور، قسمت وضعیت روغن کمپرسور، دمای سافت استارتر کمپرسور، آلارم ها و یا خطاهای سافت استارتر در طول 48 ساعت گذشته. میزان فشار خروجی کمپرسور، دمای خروجی طبقات مختلف کمپرسور، تعداد روشن و خاموش شدن موتور کمپرسور.
- مهمترین پارامترهای کمپرسور عبارتند از: زمان کارکرد سامانه در هر برج، تعداد کارکرد هر جک پنوماتیک، دمای هیتر، دمای خروجی کار از مواد دیسکانت، میزان رطوبت گاز خروجی و میزان فشار گاز ورودی.
- مهمترین پارامترهای دستگاه F8G عبارتند از: میزان نشت گاز از واحد یک، میزان نشت گاز از واحد دو، وضعیت آشکاساز آتش واحد یک و وضعیت آشکاساز آتش واحد دو.
- مهمترین پارامترهای دیسپنسرها عبارتند از: وضعیت دیسپنسرها و میزان شارژ گاز در یک زمانی مشخص.
یکی از مهمترین کاربردهای ارسال دیتا به مرکز SCADA برنامه ریزی برای تعمیرات دوره ای است. نگهداری یک جایگاه سوخت CNG یکی از مهمترین نکات در اجرای این پروژه ملی است و مهمترین موضوع که از توقف کار یک جایگاه جلوگیری می کند اجرای یک عملیات پیشگیرانه (PM) است. برای اجرای این موضوع اطلاع دقیق از وضعیت کاری اجرای یک جایگاه اجتناب ناپذیر است.
اتوماسیون دستگاه های بسته بندی
مقدمه
یکی از مهمترین صنایع کشور که می تواند ارزش افزوده بسیاری داشته باشد، صنعت بسته بندی است. تمام فرآورده های دارویی، پزشکی، غذایی، لبنی و … در پایان فرآیند تولید نیاز به بسته بندی دارند. امروزه در کشورهای توسعه یافته هیچ فرآورده یی بدون بسته بندی مناسب مورد استفاده قرار نمی گیرد. عواملی چون مدت مصرف، رعایت مسائل بهداشتی، رعایت سالم سازی محیط زیست، سادگی حمل و نقل، سهولت در فروش و توزیع و … استفاده از بسته بندی را در پایانه یک فرآیند تولید، اجتناب ناپذیر نموده است. بنا بدلایل متعدد، در کشور ما نیز استفاده از بسته بندی مناسب الزام آور است.
دستگاه های بسته بندی نیز همانند صنایع دیگر مثل نفت، پتروشیمی، برق، خودرو و … برای ایجاد کارایی مناسب، کیفیت در تولید و بالا رفتن کمیت تولید، نیاز به اتوماسیون دارند. تقریبا می توان گفت در دهه اخیر هیچ دستگاه بسته بندی مناسب خارجی بدون سیستم اتوماسیون وارد کشور نشده است. اما متاسفانه در داخل کشور هنوز دستگاه ها بدون استفاده از اتوماسیون در حال تولید است. شاید یک دلیل این امر عدم آگاهی سازندگان دستگاه های بسته بندی از مزایای اتوماسیون صنعتی باشد.
اتوماسیون صنعتی در بسته بندی دلایل عمده استفاده از اتوماسیون در بسته بندی می تواند بصورت زیر عنوان شود:
- کنترل تمام فرآیند بصورت یکپارچه و در نتیجه ارتقای سطح کیفیت بسته بندی و یکنواختی آن
- تعیین دقیق زمان تولید و تحویل سفارش ها در وقت مناسب آن
- تنظیم سرعت بسته بندی به دلیل استفاده از نرم افزار مناسب و در نتیجه برقراری تعادل بین خطوط تولیدی سری و تنظیم میزان تولید
- تغییر آسان نرم افزار و در نتیجه تعویض خط بسته بندی برای کارخانجات چند منظوره (انعطاف پذیری در تنوع تولید)
- گزارش نتایج تولید برای سطوح بالاتر و در نتیجه اعمال تصمیمات مدیریتی مناسب جهت برنامه ریزی در تولید
- عیب یابی راحت دستگاه و در نتیجه توقف کمتر آن و بالا رفتن میزان تولید
- نگهداری و تعمیر پیشگیرانه مناسب (PM)
- جلوگیری از عملکرد خارج از تنظیم و در نتیجه کاهش ضایعات در بسته بندی
- استفاده از نرم افزار برای تعیین عملکرد دستگاه و در نتیجه کاهش وابستگی به نیروی انسانی و کاهش زمان تولید
- استقلال نحوه تولید از نیروهای متخصص در بسته بندی
- معرفی یک دستگاه بسته بندی
دستگاه های بسته بندی بسیار متنوع هستند.
تقریبا می توان گفت برای بسته بندی هر نوع محصولی یک دستگاه بسته بندی مخصوص به آن وجود دارد. البته اغلب آنها دارای یک سیستم اتوماسیون مشابه هستند. یکی از انواع دستگاه های بسته بندی معروف، دستگاه وکیوم فرمینگ
(Vacuum forming) است.
در این دستگاه ورق های نایلون PP و … به صورت رول وارد دستگاه شده و در اولین ایستگاه فرم گرفته و به شکل ظرف مناسب در می آید. این ظرف ها در ایستگاه سوم مسائل مربوط به استریل یا گندزدایی، خلاء و دوخت ظرف انجام می شود و بالاخره در ایستگاه چهارم عمل برش و شمارش انجام می شود. البته مسائل جانبی مثل توزین بسته ها یا چاپ تاریخ مصرف و … روی بسته ها نیز می تواند به این خطوط اضافه شود.
عناصر اتوماسیون
اگر چه انواع ماشین های بسته بندی از نظر ساختار مکانیکی تفاوت های زیادی با یکدیگر دارند، با این وجود از نظر سیستم های اتوماسیون تشابه زیادی میان آنها وجود دارد. اگر وجه تشابه آنها را مدنظر قرار دهیم، آنگاه عناصر اتوماسیون یک دستگاه بسته بندی عبارت خواهد بود از:
- سیستم کنترل مرکزی (PLC)
- سیستم کنترل انتقال حرکت
- سنسورهای اندازه گیری آنالوگ
- پانل اپراتوری و سیستم عیب یابی و هشدار (OP PANEL)
- انواع سوئیچ های الکترونیکی (Oplo 8 Proximily SW )
- سیستم توزین الکترونیکی (Load cell)
- سیستم چاپ الکترونیکی (Jet Printer)
چگونگی ارتباط این اجزا با یکدیگر در شکل (1) ترسیم شده است.
سیستم کنترل
روش های متنوعی برای کنترل سیستم ها و فرآیندها وجود دارد. هرکدام از این سیستم ها برای کاربردی خاص طراحی شده اند. انتخاب هر سیستم به نوع فرآیند، توجیه اقتصادی، کارایی و … بستگی دارد. از یک نظر انواع روش ها را می توان به سه دسته کلی زیر تقسیم نمود:
کنترل محلی: در این حالت هر زیرفرآیند در محل خودکنترل می شود و تنها بعضی از سیگنال های مهم به کنترل مرکزی گزارش می شود. در این روش اپراتور تنظیمات مختلف را در محل انجام میدهد. اگر چه عموما علاوه بر محل باید بتوان در قسمت مرکزی نیز این تنظیمات را انجام داد.
مدرن ترین روش برای پیاده کردن این نوع مسیتم استفاده از سیستم های DCS است.
کنترل متمرکز: تمام اجزای اتوماسیون با مرکز اصلی مرتبط بوده و فرامین مورد نظر توسط کنترل مرکزی برای تمام زیر مجموعه ها صادر می شود. اپراتور با استفاده از یک پانل مرکزی کلیه اطلاعات و تنظیمات را وارد سیستم کرده و متقابلا از همین نقطه اطلاعات موجود را دریافت می کند.
کنترل مختلط: این روش ترکیبی از کنترل محلی و متمرکز است. بدین ترتیب بعضی از حلقه های کنترل و تنظیمات در حمل انجام شده و مابقی در مرکز کنترل می شود.
در یک دستگاه بسته بندی از روش سوم استفاده می شود. کنترل بعضی از قسمت ها مستقل انجام می شود. بعنوان مثال بعضی از فرامین ورودی و خروجی جهت هماهنگ سازی کلیه اجزا با یکدیگر به مرکز کنترل وابسته است. با این وصف بهترین انتخاب برای مرکز کنترل استفاده از یک PLC مدولار است.
مزیت PLC نسبت به سیستم های کنترلی دیگر عبارتند از:
- نرم افزارهای حاکم بر PLC ساده است و به راحتی می توان آن را مورد تحلیل و تغییر قرارد داد.
- بدلیل مدولار بودن نگهداری و تعمیر آن ساده و سریع و مدون خواهد بود.
- به راحتی می توان از برنامه روی PLC، نسخه پشتیبان (back up) تهیه کرد. لذا کارفرما به شخص یا شرکت خاصی وابسته نخواهد بود.
- بدلیل یکپارچه بودن براحتی می تواند هرنوع وظیفه کنترل را برعهده گیرد.
- قابلیت ارتباط با سطوح دیگر اتوماسیون
- قیمت مناسب نسبت به سیستم های کنترلی دیگر
- یک مقایسه کلی بین روش های مرسوم کنترل در ماشین های بسته بندی در جدول آمده است.
باتوجه به مزایای PLC بعنوان کنترل مرکزی و اجزا مختلف اتوماسیون و دلایل استفاده از اتوماسیون که قبلا برشمردیم؛ می توان شاخص هایی را برای انتخاب PLC مناسب تعیین کرد. اهم این شاخص ها عبارتند از:
- PLC مدولار بوده و باید کارت های جداگانه ای برای ورودی و خروجی های دیجیتال و آنالوگ داشته باشد.
- قابلیت ارسال اطلاعات به وسیله پورت سریال به یک پانل اپراتوری
- قابلیت دریافت اطلاعات از واحدهای جانبی مثل دستگاه توزین و چاپ
- قابلیت اندازه گیری سیگنال های آنالوگ شامل دما، فشار، رطوبت و خلاء با مقیاس حداقل 10 بیتی
- سرعت مناسب برای پردازش سیگنال
- دارای تعداد ورودی و خروجی به اندازه کافی و قابل توسعه برای اضافه کردن
سیستم های جانبی
سنسورهای آنالوگ
در یک دستگاه بسته بندی مهم ترین پارامترهای آنالوگ عبارتند از: حرارت، فشار،خلاء، وزن و رطوبت. کنترل این پارامترها می تواند بصورت حلقه های مستقل یا متمرکز انجام شود. در حالت مستقل بصورت محلی تنظیم و در حالت متمرکز از OP PANEL انجام می شود. عموما بهتر است از فرستنده های حرارت، فشار، خلاء و … استفاده و سیگنال جریان یا ولتاژ متناسب را به PLC منتقل کرد. خروجی فرستنده ها باید از استاندارد جریانی 20-4 میکرو آمپر یا 20-0 ولت استفاده کند. سیگنال های آنالوگ استاندارد شده با ا ستفاده از مدل AYD وارد PLC می شود. PLC باید دارای AYD حداقل 10 بیتی باشد تا حدود 1000 سطح اندازه گیری پدید آید. ترانسمیترهای فوق با دقت های متفاوت و طبعا قیمت های متفاوت در با زار موجودند.
کنترل انتقال حرکت
یکی از مهم ترین قسمت های هر دستگاه بسته بندی سیستم انتقال حرکت آن است. در دستگاه های قدیمی تنظیم کورس دستگاه بوسیله سیستم های مکانیکی انجام می گرفت. این امر علاوه بر دقت کم و عدم تغییر کورس به اندازه دلخواه، هزینه زیادی را به سازندگان تحمیل می کرد. امروزه سیستم های انتقال حرکت کاملا الکترونیک شده و دارای دقت و کارایی بالا و قیمت تمام شده پاین هستند. در این روش با استفاده از یک درایو AC برداری (Vector) و کدکننده و سیستم PLC کورس، حرکت با دقت 1/0 میلی متر و به اندازه دلخواه انجام می پذیرد. در این سیستم بدلیل استفاده از فیدبک منفی تلرانس ثابت خواهد ماند و هرگز با یکدیگر جمع نمی شوند. بنابراین معضلی به نام اختلاف کورس در دستگاه های بسته بندی مرتفع می شود.
شکل (3) یک بلوک از سیستم پیشنهادی را ارائه داده است.
اندازه حرکت توسط اپراتور و از طریق پانل کنترل به میلی متر به PLC داده می شود و شروع حرکت با استفاده از اطلاعات سنسورهای مجاورتی و توسط PLC صادر می شود. این فرمان ها به درایو AC اجازه شروع کار را می دهد. درایو AC با سرعت و شتاب از قبل برنامه ریزی شده فعال می شود. موتور سبب حرکت زنجیر و یا تسمه و …. به اندازه تنظیم شده می شود.
کدکننده پالس های متناسبی را به PLC ارسال کرده و PLC با مقایسه تعداد پالس ها و اندازه حرکت، فرمان قطع حرکت را صادر می کند.
پانل اپراتوری
هر دستگاه بسته بندی که از روش متمرکز استفاده کند، باید دارای یک پانل اپراتوری (panel operaton) باشد. این پانل وظیفه نظارت را برعهده دارد. ارتباط بین اپراتور و سیستم کنترل از این طریق برقرار می شود.
اپراتور باید قادر باشد وظایف زیر را از طریق پانل انجام دهد:
تنظیم نقاط عمل حلقه های کنترل همانند دما و فشار. جدول شماره 2 نحوه تنظیم پارامترها را مشخص کرده است.
مشاهده مقادیر واقعی حلقه های آنالوگ (Actal) بصورت On lne
توانایی مشاهده جملات خطایاب به هنگام وقوع خطاهای تعریف شده.
نمودار جریانی از نحوه عملکرد خروجی های مهم سیستم
توانایی عیب یابی سیستم هنگام بروز عیب در اجزای مختلف دستگاه
مشاهده پارامترهایی مثل مقدار محصول تولید شده زمان کارکرد دستگاه و توقف آن
برای انجام وظایف فوق نیاز به پانلی است که حداقل از یک TEX2,LCD و پورت سریال و یک آژیر جهت هشدار و …. تشکیل شده باشد.
انواع سوئیچ ها
برای ایجاد شرایط منطقی- حفاظت از قسمت های مختلف دستگاه شمارش محصول و …. نیاز به سوئیچ هایی بدون تماس است. انواع سوئیچ هایی که می توان از آن بهره برد عبارتند از:
- سنسورهای القایی (حساس به فلز)، چشم های الکترونیکی Opta سنسوهای حساس به علائم رنگی
برای تشخیص ابتدا و انتهای جک های پنتوماتیک و هیدرولیک از سنسورهای القایی، برای تشخیص موقعیت برش و چاپ تاریخ از سنسورهای حساس به رنگ استفاده می شود. برای حفاظت دست در مکان های حساس نیز بسته به موقعیت می توان از میکروسوئیچ های مکانیکی و یا چشم های مادون قرمز استفاده کرد. برای تشخیص ایجاد و یا وجود ظرف در محل پرکننده، دوخت یا برش نیز می توان از چشم های مادون قرمز که دارای فرستنده و گیرنده هستند استفاده کرد.
امیدواریم این مقاله برای شما مفید واقع شده باشد.
برای خواندن ادامه مقاله بر روی دکمه زیر کلیک نمایید
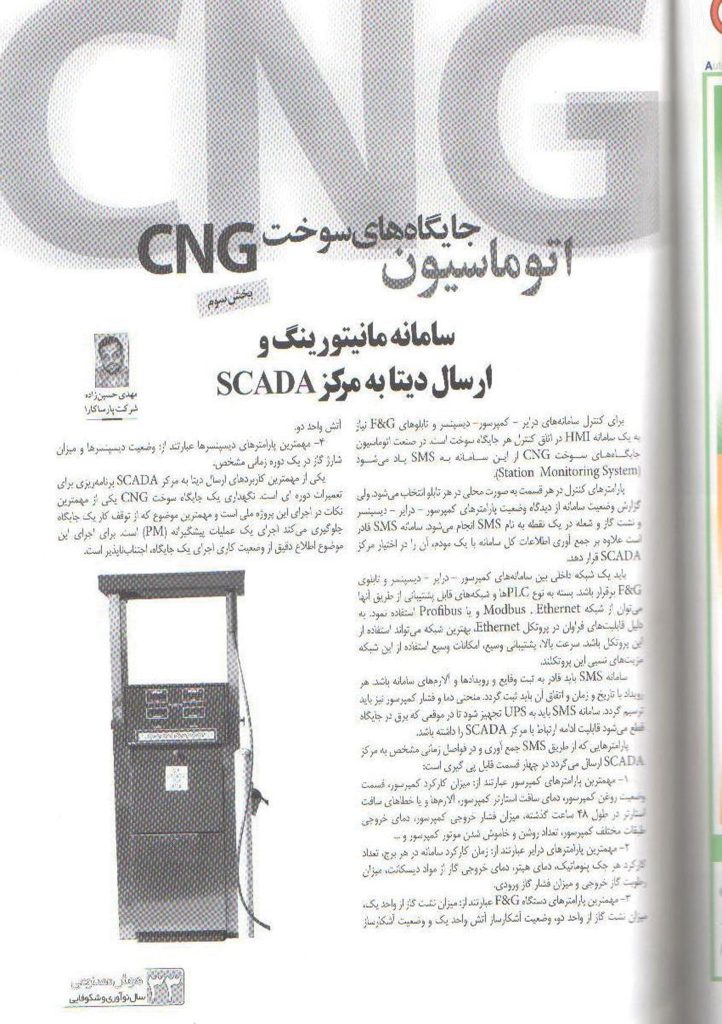