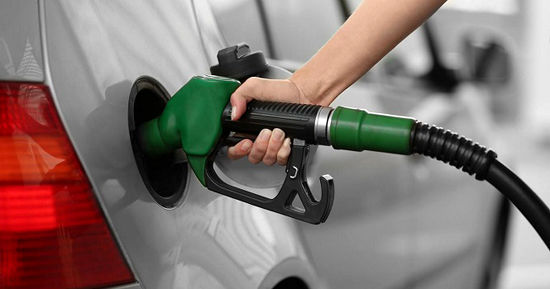
بخش نخست
در یک سوخت CNG دو فعالیت عمده صورت می پذیرد
- خشک کردن گاز شهری
- فشرده سازی گاز خشک شده جهت تزریق به اتومبیل
چون گاز شهری دارای رطوبت است باید توسط سیستم خشک کن، رطوبت گاز گرفته شده و گاز کاملا خشک با درصد رطوبت قابل قبول وارد سیستم فشرده سازی شود. یکی از روش های متداول برای خشک کردن گاز عبور آن از مواد نم گیر (دیسکانت) می باشد.
این مواد بعد از چند ساعت کار نیاز به احیا مجدد دارند. این کار باید بصورت مداوم انجام شود.
فلذا دو برج خشک کن برای این موضوع طراحی می شود؛ یکی در حال خشک کردن و دیگری در حال احیا.
چون مدار بسته است باید از گاز موجود برای مواد نم گیر استفاده شود. در قسمت فشرده سازی گاز از کمپرسور استفاده می شود. کمپرسور در 3 یا 4 STAGE عمل فشرده سازی گاز را انجام داده و گاز فشرده شده را یا بصورت مستقیم به اتومبیل تزریق می نماید یا در حالت غیر اوج کاری در کپسول های خاص ذخیره می نماید.
کنترل و اتوماسیون در یک جایگاه سوخت CNG از پنج قسمت تشکیل می شود:
- کنترل قسمت خشک کن گاز (Dryer system)
- کنترل قسمت کمپرسور (Compressor)
- 3) کنترل قسمت شارژ سوخت به اتومبیل(Dispenser)
- کنترل قسمت ایمنی شامل آشکارسازهای آتش و گاز (F8G System)
- سیستم مانیتورینگ جایگاه و اتصال به SCADA مرکزی سامانه (SMS)
اتوماسیون سامانه خشک کن (Dryer system)
برای کنترل این قسمت نیاز به یک PLC با مشخصات حداقل 16 ورودی دیجیتال 16 خروجی دیجیتال 8 ورودی انالوگ می باشد.
برای احیا یک برج و آماده سازی مواد نم گیر (دسی کانت) باید مقداری از گاز خروجی را بعنوان فیدبک به برج تزریق نمود. این کار تا حدود 200 درجه سانتیگراد گرم می شود. کنترل دمای هیترها بوسیله PLC انجام می شود. چون محیط EX می باشد برای ایجاد امنیت بالاتر، برای داغ کردن گاز علاوه بر استفاده از تجهیزات EX از یک سامانه کنترل دما بصورت موازی با PLC استفاده می شود. این سامانه تلاش دارد اگر دما از حد متعارف (حدود 250 درجه سانتیگراد) بالاتر رفت کل سیستم کنترل را خاموش نماید. سامانه کنترل PLC علاوه بر کنترل های متداول جهت ایجاد دمای لازم برای گرم کردن گاز باید الگوریتم هایی را برای جلوگیری از ورود گاز سرد به داخل برج اجرا نماید. زیرا عبور گاز سرد ترتیب احیا را مختل می نماید.
مراحل زیر برای احیای هر برج باید صورت پذیرد:
- انتخاب برج احیا
- گرم کردن گاز برای احیا (Heating Mode)
- خنک کردن برج و مواد نمگیر (Cooling Mode)
- حالت (Stand by)
وقتی سنسور رطوبت میزان مناسبی برای رطوبت گاز خروجی را نشان می دهد سامانه کنترل باید عمل سوئیچ روی برج ها را آغاز نماید. بدین ترتیب برجی که برای خشک کردن گاز استفاده می شد حال باید برای احیا آماده شود. پس از انتخاب برج احیا باید هیترها روشن شوند تا گاز را داغ نمایند. عبور گاز داغ از مواد نم گیر و در مدت زمان مشخص شده سبب احیای مواد نم گیر می شود. این زمان حدود سه ساعت می باشد. برای اینکه فشار گاز برگشتی مناسب باشد باید بوسیله موتور دمنده (Blower) گاز از میان هیتر عبور داده شود. این گاز پمپ شده از میان مواد نم گیر عبور کرده و تا حد زیادی درجه حرارت خود را از دست می دهد. چون گاز برگشتی باید دوباره به مسیر اصلی باز گردد و لذا باید خنک شود. برای خنک کردن گاز از رادیات و فن خنک کننده استفاده می شود.
یکی از الگوریتم های کنترل در PLC، مانیتور کردن دمای ورودی و خروجی خنک کننده می باشد تا بدین ترتیب گاز با دمای مناسب از برج احیا خارج و به چرخه اصلی باز گردد. دور موتور دمنده باید بوسیله اینورتر کنترل شود تا میزان دبی گاز تزریقی به برج احیا و بدنبال آن افزایش احیا مناسب باشد.
برای مانیتور کردن فرآیند و تنظیم دماهای مناسب و میزان رطوبت گاز خروجی از یک سامانه HMI استفاده می شود. در HMI
باید موارد زیر بصورت کاملا واضحی مانیتور شود:
نشان دادن باز و بسته شدن شیرهای برقی و عمل میکروسوئیچ های این شیرها و اعلام آلارم در صورت عدم انطباق عمل عملکردها
مانیتور کردن دمای گاز ورودی، دمای خروجی از برج احیا، دمای گاز خروجی از لولینگ، دمای صفحات هیترها
مانیتور کردن میزان رطوبت گاز خروجی
مانیتور کردن وضعیت عملکردهای مثل هیترها، موتور دمنده و …..
ساعت کارکرد دستگاه و تعداد عمل جک های پنوماتیک جهت اعلام تعمیرات و تعویض
صفحه آلارم جهت نمایش وقوع آلارم با حفظ تاریخ و زمان وقوع و پاسخ به آن
یکی دیگر از مسائل مهم کنترل در قسمت درایر مد کاری می باشد. دو مد کاری برای درایر تعریف می شود:
- یکی حالت ثابت که در آن سوئیچ بین دو برج با توجه به سپری شدن زمان انجام می شود
- دیگری حالت خودکار که در آن علت سوئیچ میزان رطوبت در گاز خروجی برج فعال است.
بطور میانگین هر برج حدود 34 ساعت فعال است. عمل احیا حدود 8 ساعت بطول می انجامد. بنابراین هر برج پس از احیا دست کم 16 ساعت در حالتStandby باقی می ماند.
در شماره بعد به نکات کنترلی در قسمت های دیگر یک جایگاه سوخت می پردازیم.
اتوماسیون سامانه کمپرسور
مهم ترین قست در یک جایگاه سوخت CNG سامانه کمپرسور است. بسته به فشار مورد نیاز و ظرفیت مصرف در جایگاه، کمپرسورها متفاوتند. عمده این تفاوت در تعداد مراحل (Srages) فشرده سازی گاز است. در هر صورت وظیفه این ایستگاه (Simion) فشرده کردن گاز شهری خشک شده به فشار قابل تزریق برای سوخت اتومبیل است. در کنترل این فرآیند پارامترهایی مثل کنترل فشار و دمای خروجی Stage و روغن کاری کمپرسور از اهمیت خاصی برخوردار است.
دمای خروجی هر Stage اندازه گیری و بر روی نمایشگر ثبت می گردد. اگر دمای خروجی هرStage از حد تنظیم شده بالاتر رود آلارم خاموشی (Shutdown) صادر می شود. فشار خروجی هرStage نیز اندازه گیری و همانند دمای خروجی هر Stage ثبت می گردد. فشار نیز اگر از حد معینی در حد هر بالاتر رود سامانه آلارم داده، خاموش می شود. چون در هر Stage مرحله گاز خروجی Stage خیلی فشرده تر می شود. لذا تنظیم دما و فشار در بالاتر افزایش می یابد. برای کنترل وضعیت دما و فشار می توان از ترانسمیترهای انالوگ (4-20mA) و یا سوئیچ های فشار و دما استفاده نمود. بهرحال باید ابزار دقیق از نوع EX باشد و سیگنال آنها از Barierعبور نموده سپس وارد PLCگردد. لزوم حضورBarierهای دیجیتال و آنالوگ حفاظت سامانه در محیط EX است. البته بسته به نوع ابزار دقیق و درجه EX می توان در مورد لزوم یا عدم لزوم کاربرد تصمیم گرفت. نکته دیگر کنترل روغن کاری کمپرسور است که از اهمیت بالایی برخوردار است. برای انجام این موضوع از ابزار خاصی استفاده می شود. عملکرد این ابزار بدین صورت است که به ازای هر بار روغن کاری یک پالس ساخته می شود. اگر یک دقیقه بگذرد و پالس داده نشود، سامانه باید بی درنگ خاموش شود.
مطلب دیگر در کمپرسور استفاده از Sofisrararler در سامانه راه اندازی موتور است. این موضوع بدلیل راه اندازی نرم موتور کمپرسور است. در ضمن مصرف انرژی نیز کمتر خواهد شد. زیرا در راه اندازی موتورهای توان بالا جریان زیادی از شبکه گرفته می شود که این موضوع باعث پدید آمدن مشکلاتی خواهد شد. Sofisrararler علاوه بر راه اندازی نرم سامانه حفاظت کاملی نیز از موتور انجام خواهد داد. مهم ترین حفاظت جلوگیری از جریان کشی غیرطبیعی و دو فاز شدن موتور- گرم شدن بیش از اندازه موتور جابه جایی فاز در ورودی است. اگر آلارمی اتفاق بیفتد روی نمایشگر Sofistarter با کد ثبت می شود. این موضع از طریق خروجی های دیجیتال به PLC گزارش می گردد.
الگوریتم PLC این طور خواهد بود که به هنگام وقوع آلارم روی Sofisrararler به سامانه کمپروسور Shutdown می دهد. البته بهتر است برای حفاظت بیشتر از موتور PLC هم استفاده شود. بهرحال قیمت یک موتور 200KW آن هم EX ایجاب می نماید که کنترل بیشتری روی حفاظت موتور انجام شود.
نکته دیگر توقف کمپرسور است. هرگاه بهردلیلی کمپرسور متوقف گردد چه آنکه به حالت Standby برود چه آنکه بر اثر آلارمی متوقف گردد باید فشار خروجیStage های کمپرسور تخلیه گردد تا پیستون ها تحت فشار باقی نمانند. برای این موضع یک تانکی تحت Blowdown تعبیه می گردد. بنابراین در الگوریتم PLC باید به این نکته توجه نمود که بعد از توقف کمپرسور طی سیکلی، شیر برقی های خروجی Stageها به تانک Blowdown فعال شود تا گاز فشرده شده به این تانک هدایت گردد. در زمان استارت کمپرسور باید این گاز ذخیره شده به ورودی کمپرسور وارد گردد تا مجددا سیکل فشرده سازی صورت پذیرد. برای تطبیق فشار گاز در Blowdown تانک و حداکثر فشار کاری Stage یک رگولاتور مورد نیاز است.
کنترل ایمنی (Syatem G8F)
مهم ترین نکته در ایمنی یک جایگاه سوخت CNG کنترل وضعیت اشکار سازهای آتش و گاز است. حسگرهای بسیار پیشرفته که بر مبنای آشکارسازی فروسرخ و فرابنفش عمل می کنند، وظیفه آشکارسازی آتش را برعهده دارند. این ترانسمیتر تمام وضعیت خود را با سیگنال 20-4 میلی آمپر گزارش می نماید. بعنوان مثال اگر در تغذیه مشکلی ایجاد شود 5 میلی آمپر ارسال می نمایند. حسگرها طیف نور (مادون قرمز- ماورای بنفش) را با سیگنال های متفاوت ارسال می نمایند. ارسال 20 میلی آمپر به معنای وقوع آتش است. این ترانسمیتر باید درون محفظه نصب کمپرسور و یا درایر قرار گیرد و معمولا برای Dnit یک عدد ترانسمیتر طراحی می شود.
علاوه بر ترانسمیتر آشکارسازی آتش، سنسورهای آشکارسازی دود نیز باید در اطراف جایگاه تعبیه شود. به هنگام بروز دود در اطراف جایگاه باید آلارم اضطراری فعال شود. مسئله مهم دیگر در ایمنی جایگاه سوخت، آشکارسازی نشت گاز است. ترانسمیترهای دقیقی برای این موضوع وجود دارد که می تواند نشت گاز را با دقت DEL01 حس نماید و با سیگنال 20-4 میلی آمپر به PLC گزارش نماید. در الگوریتم PLC باید نشت بیش از DEL 20% بعنوان وضعیت خطرناک در نظر گرفته شود و کمپرسور جریان برقش را قطع نماید.
تابلوی F8G باید از سامانه کنترل کمپرسور و درایر جدا باشد و دست کم استاندارد EN 52 را داشته باشد. برای آنکه در هنگام قطع برق همجنان نظارت بر آتش و نشت گاز باشد و یا به هنگام بروز آتش و یا نشت گاز PLC فرمان قطع برق ورودی به تابلوهای کمپرسور و درایر می دهد. باید تابلوی F8G به USP مجهز باشد.
امیدواریم این مقاله برای شما مفید واقع شده باشد.
برای خواندن ادامه مقاله بر روی دکمه زیر کلیک نمایید
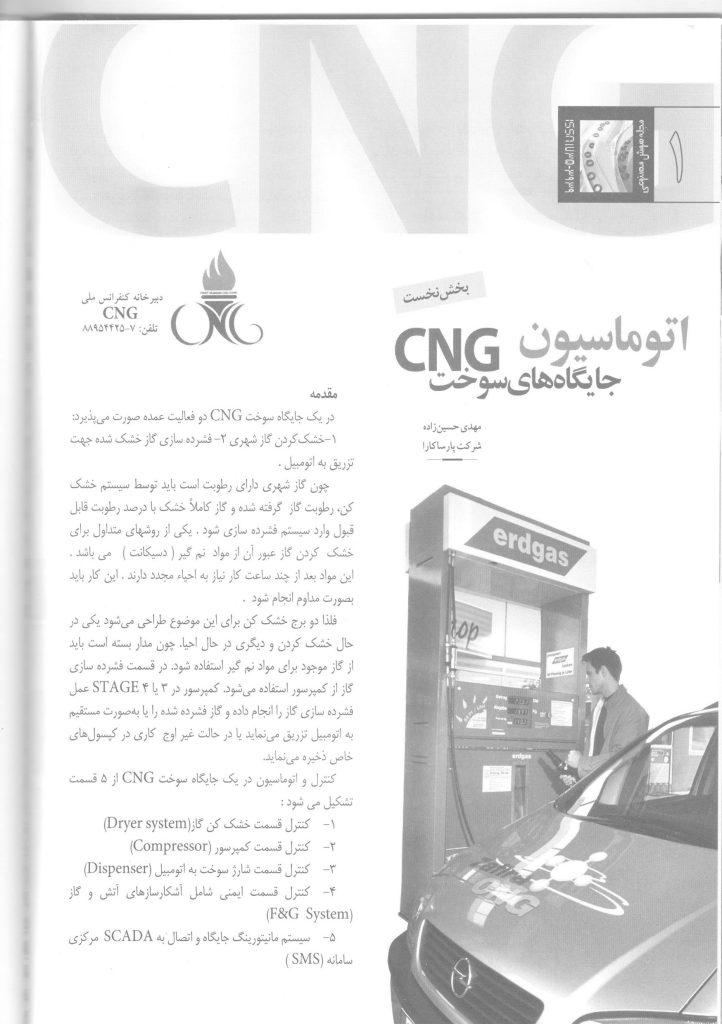
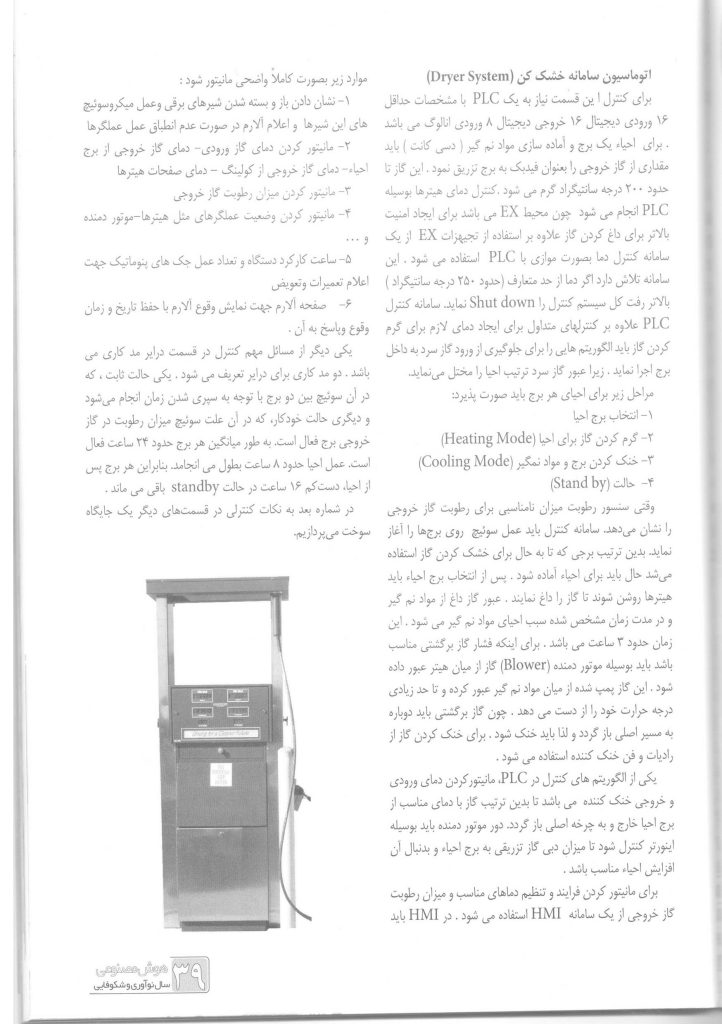